Vanceer understands that electronic components are the most basic components of a product, and their quality level will have a critical impact on the stability and reliability of the whole system. Electronic component screening is a series of short-term environmental stress accelerated test and test technology, the entire batch of electronic components for non-destructive testing, to select the characteristics of qualified components or determine whether the batch of products qualified to receive, to improve the reliability of product use.
What is the importance of component screening?
Electronic components are electronic components and electrical small parts of machines and instruments, which itself often consists of a number of parts, can be common in the same kind of products; often refers to electrical, radio, instrumentation and other industrial parts, such as capacitors, transistors, tour wire, clockwork and other sub-devices of the general term. Commonly, there are diodes and so on. Components are the basis of the whole machine, and the inherent reliability of electronic components depends on the reliability design of the product, which may form time- or stress-related failures in use due to its inherent defects in the manufacturing process or improper control of the manufacturing process. In order to ensure the reliability of the whole batch of components, electronic components should be installed on the whole machine, equipment before, we should try to have early failure of the components to exclude as much as possible, for this purpose, we have to screen the components.
The inherent reliability of electronic components depends on the reliability design of the product. In the manufacturing process of the product, due to human factors or fluctuations in raw materials, process conditions and equipment conditions, the final product may not all reach the expected inherent reliability. In each batch of finished products, there are always some potential defects and weaknesses in some of the products. These potential defects and weaknesses, under certain stress conditions, are manifested as early failures. The average life of components with early failure is much shorter than normal products. Therefore, the screening of components is very important and necessary.
Testing Service
1.Appearance Testing
Description: Appearance testing refers to confirming the number of chips received, the inner packaging, humidity indication, desiccant requirements and proper outer packaging. Next, the appearance of individual chips is inspected, mainly including: the typing of the chip, the year, the country of origin, whether the chip is recoated, the state of the pins, whether there are re-polishing traces, unknown residues, and the location of the manufacturer's logo.
Application scope: According to the relevant testing standards, determine whether the chip is brand new, whether it is refurbished, whether the pins are tinned, oxidized, etc.


2.Solderability test
Description: According to the test standard of the solderability test, this test mainly detects whether the solderability of the chip pins is up to standard.
Solderability test purpose and significance:
a. Solderability test is generally used to make a qualitative and quantitative assessment of the solderability of components, printed circuit boards, solder and flux. In the assembly and soldering process of electronic products, the solder quality directly affects the quality of the whole machine. Therefore, in order to improve solder quality, in addition to strict control of process parameters, scientific solderability testing of printed circuit boards and electronic components is required.
b. By implementing the solderability test, we help companies to determine the goodness of the solderability and the quality of the products after production and assembly. In practical operation, it further enriches the technical means of solderability testing of printed circuit boards and other components, clarifies the intrinsic factors affecting solderability, and gives great help to technical engineers in the manufacturing industry to improve product quality and zero-defect soldering processes.

3.Slicing Test
Description: Cross-section, X-section, is one of the most common means of sample preparation and analysis to observe the cross-sectional structure of a sample. It is commonly used in PCB/PCBA, parts and other manufacturing industries for quality determination and quality abnormality analysis, inspection of circuit board quality, PCBA soldering quality inspection, finding the causes of failure and solutions, evaluating process improvement, and as a basis for objective inspection, research and judgment, and is also one of the common means of chip failure analysis.

4.Chemical uncapping
Description: Open cover (unsealing) is mainly used to corrode the package on the surface of the chip, check whether there is a wafer inside, the size of the wafer, the manufacturer's logo, the copyright year, the wafer code, can determine the authenticity of the chip. Applications: Verification of chip authenticity and failure analysis, etc.

5.Failure analysis
Failure analysis significance:
a. Provide the basis for electronic component design and process improvement, and guide the direction of product reliability work.
b. Identify the root cause of electronic component failure, and effectively propose and implement reliability improvement measures.
c、Improve the finished product yield and reliability, and enhance the core competitiveness of enterprises.
d、Define the responsible party for causing product failure, and provide the basis for judicial arbitration.
The types of components analyzed: integrated circuits, field-effect tubes, diodes, light-emitting diodes, transistors, thyristors, resistors, capacitors, inductors, relays, connectors, optocouplers, crystal oscillators and other active/passive devices.
Main failure modes (but not limited to: open circuit, short circuit, burnout, leakage, functional failure, electrical parameter drift, non-stationary failure, etc.
6.X-Ray inspection
Description: For the chip can not be directly detected by the appearance of the location, the use of X-Ray penetration of different densities of material and its different light intensity changes, the resulting contrast effect can form an image, you can show the internal structure of the object to be tested, and thus achieve the chip internal defects without damaging the sample to be tested, nowhere to hide.
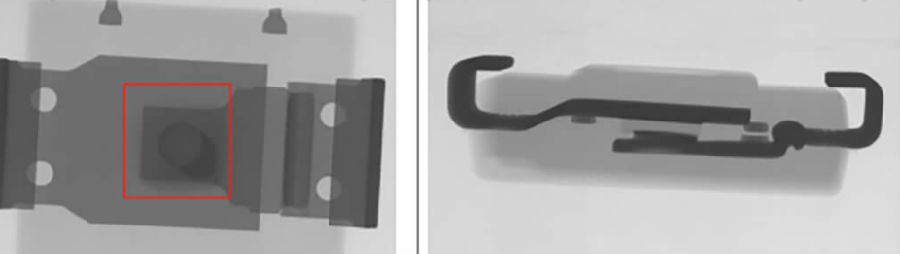
7.Ultrasonic scanning
Description:Using ultrasonic pulses to detect the presence of voids / delamination / cracks inside the sample
8.Ambient Temperature Testing
Description:
1, ambient temperature test, simulate all kinds of extreme environment has many effects on the product, such as reliability, oxidation, chemical changes, thermal diffusion, electromigration, metal migration, melting, vapor deformation, etc. Usually every 10 ℃ rise in the surrounding environment, the product life will be reduced to a quarter; when the ambient temperature rises 20 ℃, the product life will be reduced by half, the product life follows "10 ℃ rule", thus the high temperature test as a super common test, used for the screening of components and the whole machine, reliability test, life test, accelerated life test, while playing an important role in the verification of failure analysis.
2, similarly, low temperature also has many effects on the product, such as embrittlement, icing, viscosity increase, curing, control of mechanical strength and physical shrinkage, etc. The low temperature test is used to assess the adaptability of the product for storage and use in low temperature environment, and is commonly used in the development stage of the product type test, component screening test, etc.
9.Electrical performance test
Description: According to the electrical characteristics of the component specifications, the use of semiconductor test equipment through static, open circuit, short circuit parameters to detect whether the chip is bad or damaged.
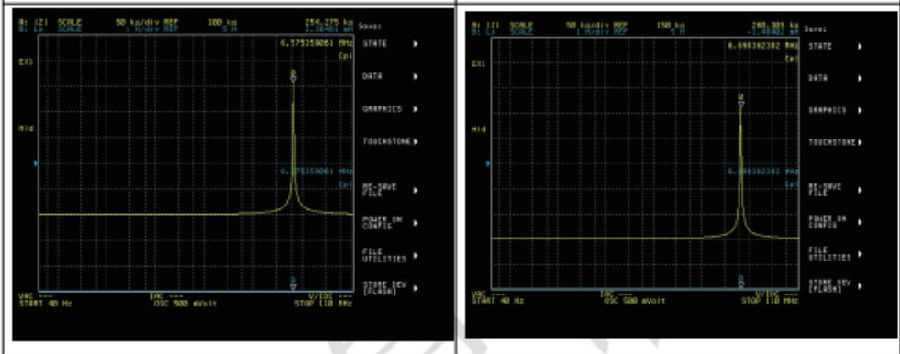
QC Process:
1.Submit an application
2.System Preliminary Review
3.Sending samples
4.QC Inspection
5.Issuance of reports
Need Customer Service? Click here to contact our Customer Service Team